Selected Features of BQ Wire Cut EDM Machine
- Display CPU board uses industrial-grade motherboard, embedded Win10 operation system, SSD solid-state electronic disk, which can turn off at any time, the system never crashes.
- Advanced pulse power and anti-electrolysis power technology, improving the dimension accuracy and cutting accuracy of the parts.
- THK/PMI/HIWIN high precision linear guide, ball screw, super quality bearing from NTN Japan/FAG Germany, mechanical precision maintaining for long lifetime.
- Mitsubishi servo system, equipped with 5-axis MPG, which makes machine movement fast and smart.
- X、Y、U、V、Z 5-axis numerical control, with the function of automatic edge finding, automatic center finding, etc.
- BQS Series
- BQ Series
- BQY Series
- Certificates
Parameters | BQS400 | BQS650 |
Worktable size(mm) | 735×460 | 1000×540 |
X/Y travel(mm) | 400×320 | 650×450 |
Max workpiece size(mm) | 800×500 | 1200×650 |
Max cutting thickness(mm) | 300 | 300 |
Max load weight(kg) | 400 | 600 |
U/V travel(mm) | 36×36 | 36*36 |
Max cutting taper | ±9°/100mm | ±9°/100mm |
Control type | X Y Servo,UVZ hybrid motor | X Y Servo,UVZ hybrid motor |
Z transmission | Numerical control | Numerical control |
Simultaneously Controlled axes | X Y U V-4 Axis | X Y U V-4 Axis |
Wire diameter(mm) | Φ0.1-Φ0.2 | Φ0.1-Φ0.2 |
Wire speed (m/s) | 1-11.4 | 1-11.4 |
Reposition accuracy(mm) | ≤±0.003 | ≤±0.003 |
Max cutting speed (mm2/min) | ≥300 | ≥300 |
Roughness/Ra(um) | 0.7-1.4 | 0.7-1.4 |
Water tank volume(L) | 150 | 150 |
Filtering method | 3 layer filtration | 3 layer filtration |
Power supply | Three phase 380V AC/50Hz | Three phase 380V AC/50Hz |
Control system | Baqi system | Baqi system |
Total power consumption(kw) | 1.6 | 1.6 |
Max machining current(A) | 10 | 10 |
Machine gross weight(kg) | 1800 | 2300 |
Machine size(mm) | 1700x1200x2000 | 2300*1900*2080 |
Top-bottom abnormity cutting | Yes | Yes |
Parameters | BQ400 | BQ500 | BQ630 | BQ800 |
Worktable size(mm) | 735×460 | 836×550 | 935×645 | 1120×800 |
X/Y travel(mm) | 400×320 | 500×400 | 630×500 | 800×630 |
Max workpiece size(mm) | 800×500 | 980×600 | 1140×730 | 1300×840 |
Max cutting thickness(mm) | 300 | 300 | 300 | 380 |
Max load weight(kg) | 400 | 600 | 900 | 1400 |
U/V travel(mm) | 80×80 | 80×80 | 80×80 | 80×80 |
Max cutting taper | ±15°/150mm | ±15°/150mm | ±15°/150mm | ±15°/150mm |
Control type | Mitsubishi Servo , UVZ hybrid motor | Mitsubishi Servo , UVZ hybrid motor | Mitsubishi Servo , UVZ hybrid motor | Mitsubishi Servo , UVZ hybrid motor |
Z transmission | Numerical control | Numerical control | Numerical control | Numerical control |
Simultaneously Controlled axes | X Y U V-4 Axis | X Y U V-4 Axis | X Y U V-4 Axis | X Y U V-4 Axis |
Wire diameter(mm) | Φ0.1-Φ0.2 | Φ0.1-Φ0.2 | Φ0.1-Φ0.2 | Φ0.1-Φ0.2 |
Wire speed (m/s) | 1-11.4 | 1-11.4 | 1-11.4 | 1-11.4 |
Reposition accuracy(mm) | ≤±0.003 | ≤±0.003 | ≤±0.003 | ≤±0.005 |
Max cutting speed (mm2/min) | ≥300 | ≥300 | ≥300 | ≥300 |
Roughness/Ra(um) | 0.7-1.4 | 0.7-1.4 | 0.7-1.4 | 0.7-1.4 |
Water tank volume(L) | 150 | 150 | 150 | 150 |
Filtering method | 3 layer filtration | 3 layer filtration | 3 layer filtration | 3 layer filtration |
Power supply | Three phase 380V AC/50Hz | Three phase 380V AC/50Hz | Three phase 380V AC/50Hz | Three phase 380V AC/50Hz |
Control system | Baqi system | Baqi system | Baqi system | Baqi system |
Total power consumption(kw) | 1.6 | 1.7 | 1.8 | 2 |
Max machining current(A) | 10 | 10 | 10 | 10 |
Machine gross weight(kg) | 2100 | 2600 | 3600 | 4200 |
Machine size(mm) | 1300x1550x1920 | 1550x1770x2050 | 1580x1820x2050 | 2090*2330*2580 |
Top-bottom abnormity cutting | Yes | Yes | Yes | Yes |
Parameters | BQY400 | BQY500 | BQY630 |
Worktable size(mm) | 735×460 | 836×550 | 935×645 |
X/Y travel(mm) | 400×320 | 500×400 | 630×500 |
Max workpiece size(mm) | 800×500 | 980×600 | 1140×730 |
Max cutting thickness(mm) | 300 | 300 | 300 |
Max load weight(kg) | 400 | 600 | 900 |
U/V travel(mm) | 80×80 | 80×80 | 80×80 |
Max cutting taper | ±15°/150mm | ±15°/150mm | ±15°/150mm |
Control type | X Y Z U V W 6 axis servo | X Y Z U V W 6 axis servo | X Y Z U V W 6 axis servo |
Z transmission | Numerical control | Numerical control | Numerical control |
Simultaneously Controlled axes | X Y U V-4 Axis | X Y U V-4 Axis | X Y U V-4 Axis |
Wire diameter(mm) | Φ0.1-Φ0.2 | Φ0.1-Φ0.2 | Φ0.1-Φ0.2 |
Wire speed (m/s) | 1-11.4 | 1-11.4 | 1-11.4 |
Reposition accuracy(mm) | ≤±0.003 | ≤±0.003 | ≤±0.003 |
Max cutting speed (mm2/min) | ≥300 | ≥300 | ≥300 |
Roughness/Ra(um) | 0.7-1.4 | 0.7-1.4 | 0.7-1.4 |
Water tank volume(L) | 150 | 150 | 150 |
Filtering method | 3 layer filtration | 3 layer filtration | 3 layer filtration |
Power supply | Three phase 380V AC/50Hz | Three phase 380V AC/50Hz | Three phase 380V AC/50Hz |
Control system | Baqi system | Baqi system | Baqi system |
Total power consumption(kw) | 1.6 | 1.7 | 1.8 |
Max machining current(A) | 10 | 10 | 10 |
Machine gross weight(kg) | 2100 | 2600 | 3600 |
Machine size(mm) | 2100x1680x2100 | 2360x1870x2160 | 2398x1938x2180 |
Top-bottom abnormity cutting | Yes | Yes | Yes |
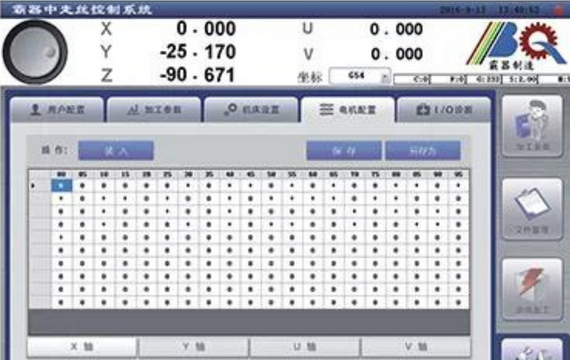
Advantages of BQ Wire Cut EDM
- Easy to install. Operation interface adopts multiple artificial intelligence algorithm, simple for beginner to master in a short time.
- Power off protection. It can memorize machining status automatically when sudden power off, and continue to process when power supply recover.
- Automatic center finding. Spark center finding by one key, do not need to memorize the coordinates, it can back to center automatically.
- Remote control box can set reference starting point and halfway, XYUVZ 5axis digitial display.
Advantages of BQ Wire Cut EDM
- Z-axis adopts high precision linear guideway, it can memorize machining position automatically and driven by motor, can be moved up and down freely.
- After programming, the offset can be modified at any time, does not need to be reprogrammed.
- If the hole threading in the wrong place leads to short circuit, user can move it to the right position, it can back to the starting point to finish cutting.
- During machining, users can set new offset according to the moly wire loss, do not need to stop current machining.
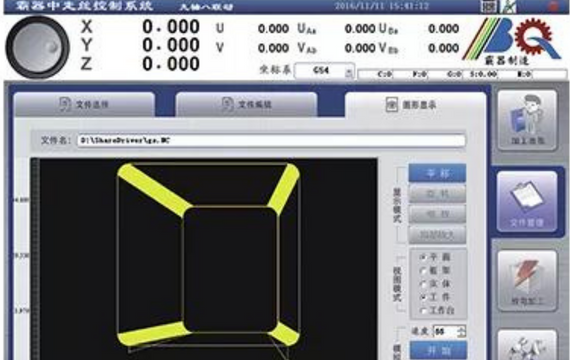
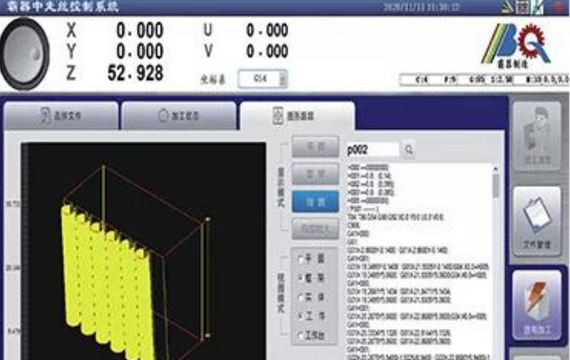
System Function
- Mirror machining, single-stage machining, program editing, automatically machining condition convert.
- Return halfway, automatic edge finding, wire alignment, subprogram calling, back to the origin point and suspension point.
- Proportionally scaling, top-bottom abnormality cutting, automatic wire radius compensation.
- Simulation check, pitch compensation, automatic center finding, graphic real time tracking and check, unmanned processing (power-off after finishing).
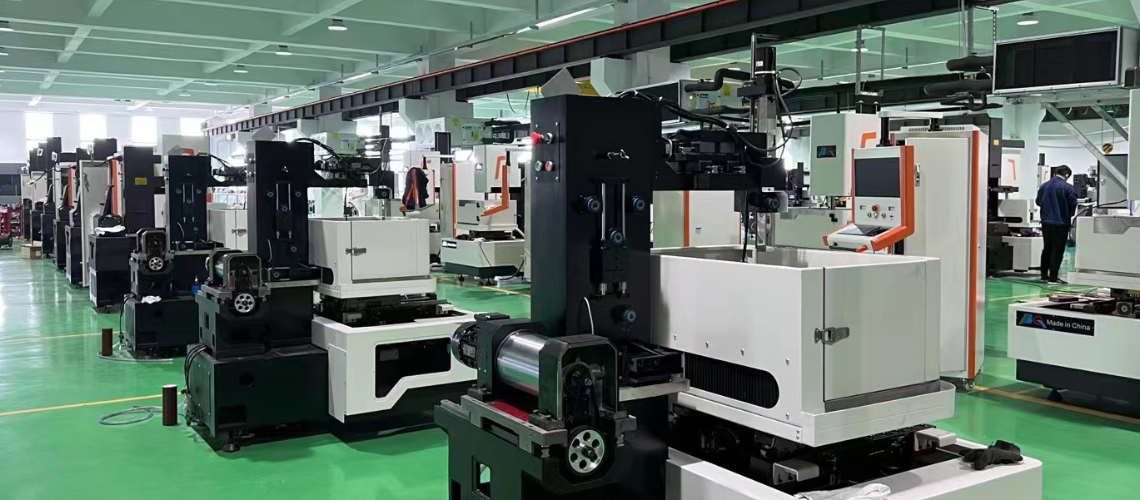
How to do daily maintenance of wire cut EDM?
The daily maintenance of wire cut EDM is very important, that is related to the service life of the machines, users should pay attention to regular maintenance to prevent the expansion of small problems and affect the normal use of the edm machines. When overhauling, the focus should be on the following four parts:
- Power supply : Check the input power supply of the wire EDM, whether the voltage fluctuation is within ±10%, whether the higher harmonics are serious, and the size of the power, whether it is necessary to install a stabilized power supply, etc.
- Working fluid: The role of the wire edm working fluid is cooling, washing, chip removal, etc. Therefore, the qualification of the wire edm working fluid is directly related to the quality of the workpiece. Check whether the wire-cutting fluid is too dark or smelly. If this phenomenon occurs, its overall performance will become poor and it will easily lead to wire breakage.
- Electrode wire: The quality of the workpiece is directly affected by the quality, installation and storage of electrode wire. Check whether the electrode wire is choosed properly, thicker electrode wire should be used for processing thick workpieces, which is beneficial to chip removal, check the tightness of the electrode wire installation, when the electrode wire is too loose, the electrode wire will shake badly and it will be easy to break. If it is too tight, the internal stress will increase, and the wire will be easily broken, check whether the electrode wire installation position deviates from the center or are not in the same plane. If so, the electrode wire is easily broken or pinched, check whether the storage of the electrode wire is standard, If there is damp, oxidized, or exposed to the sun during storage, the electrode wire will become brittle and break easily.
- Control cabinet: Dust is easy to accumulate in the wire edm control cabinet due to static electricity and other reasons. When the dust is damp, it will corrode the circuit board, cause short circuit or open circuit, and then damage the electronic components, and even cause the entire circuit board to be scrapped. Therefore, it must be checked regularly.
Send Your Inquiry Today